As pioneers in the field of dip molding, StockCap benefits from over 70 years of experience in compounding vinyl plastisol formulations. This experience is what makes us different from other plastisol coating suppliers. If you have an interest in the plastisol coating process, let our experience assist. We offer free consultations. Our plastisol formulas are branded under the name VynaFlex®.
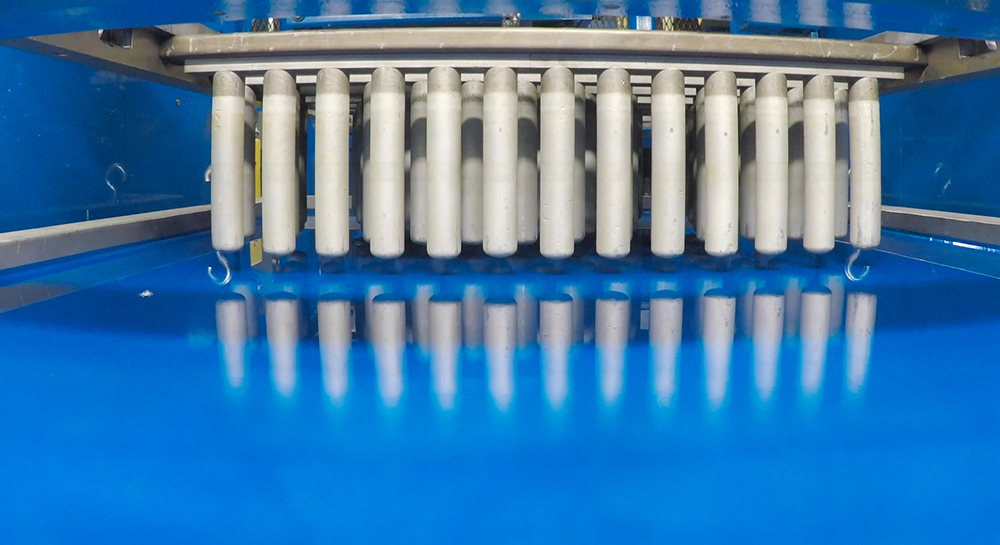
Why Work with Us
While the concept of dip molding and dip coating processes are generally understood, the crucial knowledge is found in experience running dip molding or coating equipment.
As plastisol compounders, our engineers and chemists understand the complexity of this process and have first hand knowledge of how to manage both the pre-heat and curing processes, the agitation of the material, and the consistency of material temperature.
While there are many uses for PVC plastisol, our primary focus is on manufacturing plastisol for the dip coating and dip molding industries.
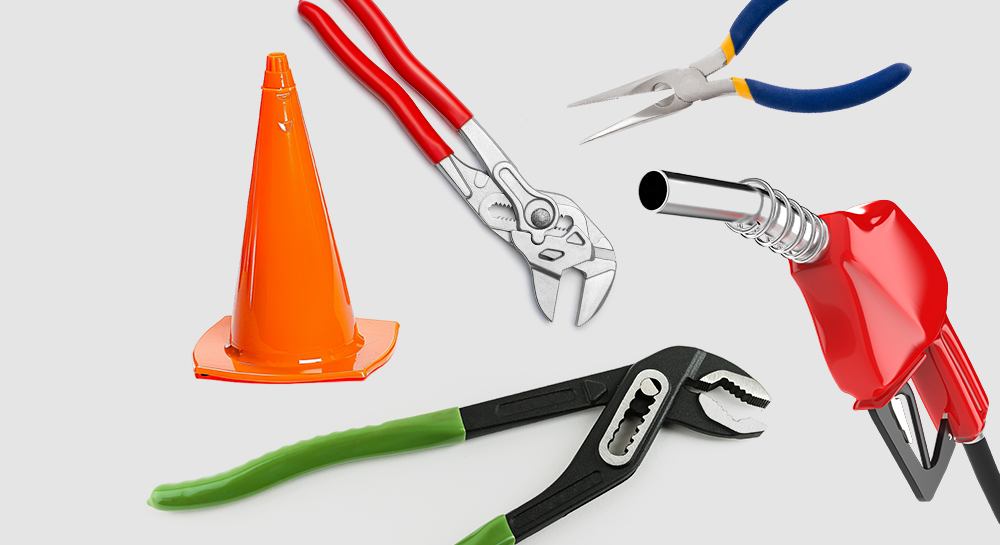
Typical Applications
Plastisol can be used as a protective coating in a wide variety of applications including:
- Hand Tools & Handles
- Marine Products
- Outdoor Playground Equipment
- Outdoor Furniture
- Electrical Insulation Covers
- Gas Nozzles
- Safety Cones
Custom Formulas
As one of the largest plastisol compounders in the world, we have the capacity and experience to supply a wide variety of formulas. We can manufacture virtually any color desired in a wide variety of surface textures with a wide range of features.
Our specialists will work closely with you to understand your product requirements. Then, using our state-of-the-art laboratory, our chemists will engineer a plastisol formulation for your review and testing.
Standard Formulas
Our sister company, GripWorks, also offers the VynaFlex® brand in three primary formulas, in three standard colors, packaged in cans, pails or drums.
Standard (701) – Soft and flexible vinyl with a smooth finish
Basic Semi-Rigid (750) – Slightly rigid material with a smooth finish
Textured (325) – Soft and flexible material with a coarse finish
Standard Colors
Each of these materials is available in black (89), red (1R) and blue (53).
Packaging Options (Available from GripWorks)
Each one the formula/color combinations above can be purchased in cans, pails or drums. You can learn more at GripWorks.com
How to Use Plastisol for Dip Molding Applications
Originally used in the art of candle making, dip molding has grown into a high-tech manufacturing method that competes head to head with other plastic and rubber molding processes. In its basic form, dip molding involves:

1) The heating of a part or metal mold with the internal dimensions of the desired part

2) The heated part or molds are then immersed or “dipped” in a tank of liquid plastisol (PVC)

3) The heat from the mold attracts the cool plastisol and the part is formed

4) The molds are extracted from the liquid and heat cured

5) After the material is cured, cool the parts